
Mill Bolting



“Do it right and do it once”
If your company has a grinding mill or are going to install a mill in the future, then the saying above, “says it all”, unfortunately for all involved, too many companies don’t follow these words.
As grinding mill get bigger the associated problems get larger, we provide a complete service to tighten all the critical fasteners of your mill to the required tolerances providing usable up to date data that can be used for the life of your mill. Whether it’s the critical fasteners holding the shell together of the liner bolts, they will both impact on your mines ability to run at full production.
technicians have been called to many sites, to correct problems that shouldn’t have happened. These problems could have been avoided if the mine owners and construction companies had given bolting the time and respect it deserves.
The pictures below are just some of the major bolting issues that our technicians have come across.

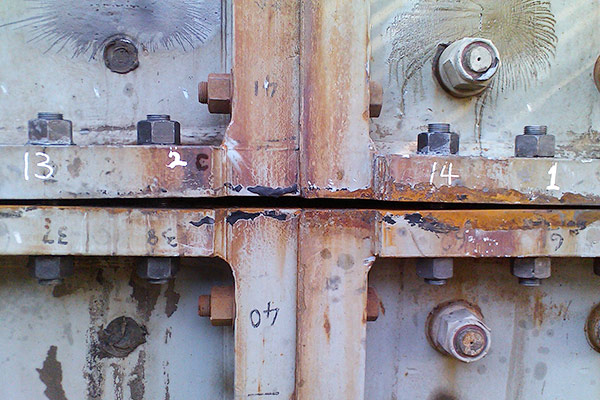
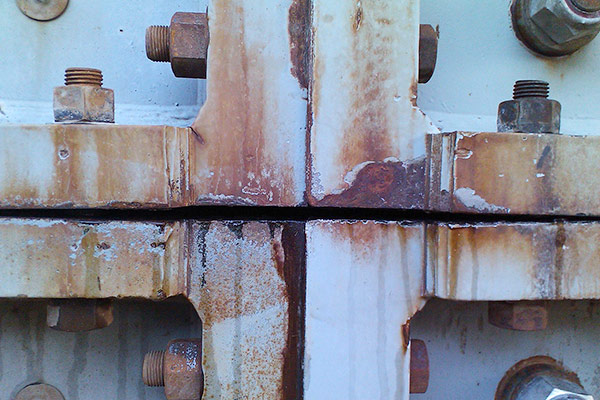
This Mill was just two years old


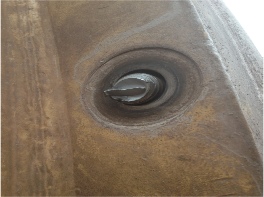
This Mill had 33 consecutive bolts broken, the flange only had 68 bolts, almost half were missing this Mill is 4 years old and the problems started just 4 months after commissioning.
Our company helps in prolonging the life of your mills by providing a complete service to record the load in your bolts and adjust them if necessary, returning your bolts back to the required tolerances.
Our service includes tools, equipment, experienced Ultrasonic bolting technicians and verifiable inspection reports.
Boltprep provides highly skilled and experienced Technicians who are trained to identify bolted joint issues before they become critical, we initiate corrective actions to help our customers to implement programs and processes to prevent premature breakdowns.
The trouble with torque is it can be 25% to high or 25% to low, there can easily be a variance of 50% between adjacent bolts.
When a mill is commissioned, the construction company should make sure that all the bolts are tightened to the correct load / torque to keep the flange joint tight and together during operation.
This load should be checked and verified.
The mill manufacturer specifies a load which is designed to be the optimum load applied to the bolts to hold the mill together for its entire life, which can be in excess of 20 years, some mill manufacturers specify an elongation, unfortunately they usually specify a torque figure which should in a best case produce the correct elongation, but rarely does.
Torque alone should never be used for this application
Torque in basic terms is the force multiplied by the distance needed to overcome the friction created between the mating faces and parts of a fastener.
If your contracting company uses torque and is very diligent in the application of their bolting techniques, you could only end up with a mill which has 50% of the bolts doing 100% of the work and all this before a single liner or the weight of the ore and grinding media are introduced.
Bolts by their very nature are designed to undo, from the very moment the load used to tighten a bolt for the very first time is released, a bolt starts to loosen, it can loose anywhere from 10-20% of its load in the first 48 hours and that’s without the normal bedding in process.
This is why a re-torque is specified and is usually carried out, (mostly seen on liner bolts), but what about the bolts holding the mill together?, All to often they are just overlooked, and the results can be seen above.
When the mill finally goes into operation the structural bolts on mills are exposed to extreme loads during operation and after a period of time they start to relax and loosen off further, this can lead in a surprisingly short time to joint leakage and eventually failure.
Our aim is to educate mill owners and give them a way to stop this happening, we provide a service where we record the actual load in each and every individual bolt while the mills are constructed making sure that the mill owners have a record of the correct load in each bolt, before the mill enters production.
When your mill goes into production we are able to periodically come back and adjust your bolts back to the required load needed to keep the joints securely fastened, these regular checks enables us to look for potential problems and gives you the opportunity to rectify them before they turn into costly down time.